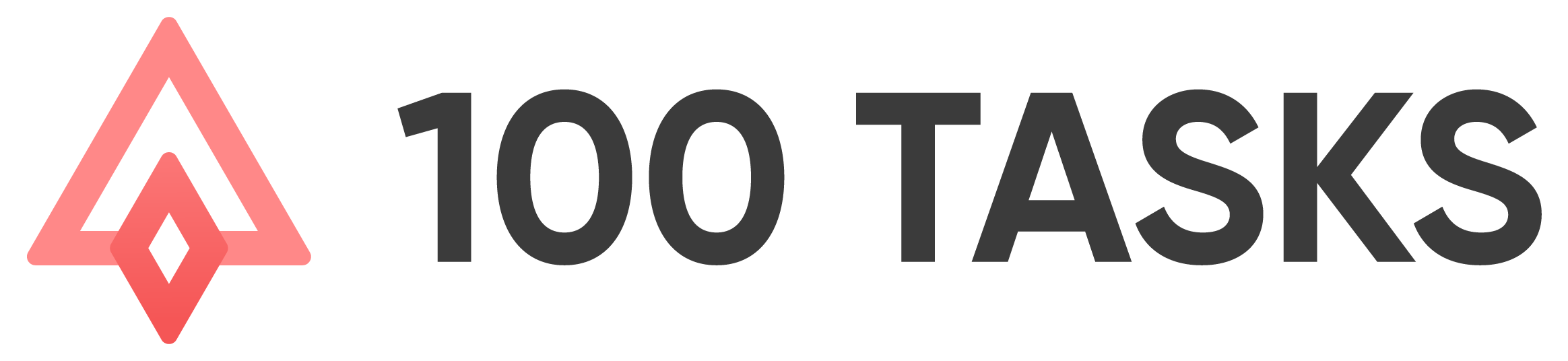
Systematically Build Your Startup. Fast.
Democratizing Entrepreneurship through a Proven Venture Building Process.
Democratizing Entrepreneurship through a Proven Venture Building Process.
100tasks@bell.ventures
Schedule a Demo Call
Imagine a world where your business processes run smoothly, defects are minimized, and customer satisfaction reaches new heights. Sounds like a dream, right? It doesn’t have to be. Six Sigma tools can transform that dream into reality. With these powerful techniques at your disposal, you can revolutionize your organization’s approach to quality control and process improvement, just like we’ve done for over 20,000 startups with our proven 100 Tasks Company Builder Program
Six Sigma tools can redefine your organization’s success. Adopting a data-driven approach and striving for continuous improvement enhances business processes, minimizes defects, and boosts customer satisfaction. Six Sigma methodology focuses on:
This ensures high quality and efficiency in your organization.
Project management tools such as regression analysis, process mapping, and root cause analysis play a pivotal role in achieving successful Six Sigma initiatives. Moreover, qualitative and quantitative techniques play a vital role in driving process improvement, ensuring high-quality outcomes, and fostering customer satisfaction.
In today’s fast-paced business environment, instinctive decisions are insufficient. Six Sigma tools utilize a data-driven approach, identifying and eliminating process variations to enhance overall performance and customer satisfaction. The DMAIC methodology is a prime example of Six Sigma’s data-driven approach, utilized to improve existing products or services and achieve customer satisfaction.
DMADV, another key component of Six Sigma, is employed to design or re-design processes of product manufacturing or service delivery, executed by Six Sigma Green Belts and Black Belts under the supervision of Master Black Belts. Utilizing these methodologies, Six Sigma practitioners can effectively address process variations, ensuring that the organization stays on the path to success.
Any organization aiming to reach new heights must foster a culture of continuous improvement. Six Sigma tools facilitate this culture, constantly refining processes and striving for excellence. Kaizen, a key element of continuous improvement, involves:
Implementing Six Sigma principles and methodologies enables your organization to cultivate a culture supporting continuous improvement, and delivering sustainable results. The implementation of Statistical Process Control (SPC) and Failure Modes and Effects Analysis (FMEA) are examples of Six Sigma techniques that can significantly enhance your organization’s quality control and reduce defects.
Mastering the top 10 tools for process improvement is vital to truly unlock the potential of Six Sigma. These tools, comprising statistical and graphical tools, drive process improvement and enhance overall performance. By employing these tools, organizations can make data-driven decisions, effectively address process variations, and ensure a high level of quality control.
The selection of the right Six Sigma tools is dependent on the specific needs and goals of your organization. Understanding the unique requirements of your organization and industry allows you to select the most suitable tools for driving process improvement, enhancing customer satisfaction, and achieving success.
Value Stream Mapping, also known as value stream map, is a powerful Six Sigma tool that helps organizations visualize and analyze their processes, identifying waste and inefficiencies that can be eliminated to create more efficient production processes.
Constructing a visual representation of all the components required to deliver a product or service allows organizations to scrutinize and optimize the entire process, enhancing overall performance and customer satisfaction.
Cause and Effect Analysis, also known as Fishbone Diagram, is a vital tool in the Six Sigma process improvement arsenal. This graphical tool displays a list of causes related to a particular effect, helping improvement teams identify the root causes of a problem and make data-driven decisions for process improvement.
Employing Cause and Effect Analysis enables organizations to address the underlying issues impacting their processes effectively, resulting in enhanced performance and customer satisfaction.
The 5 Whys technique, a root cause analysis tool used in the Analyze phase of the Six Sigma DMAIC methodology, assists in identifying the underlying causes of a problem by posing the question “why” five times.
Drilling down to the root cause of an issue enables organizations to:
The Kanban System is a supply chain control system that focuses on cost reduction. It does this by implementing a just-in-time inventory control system. Initiating the supply chain only when demand necessitates it allows the Kanban System to help organizations:
The Kanban System is designed to reduce inventory costs by eliminating the need to store excess inventory
The Pareto Chart is a powerful Six Sigma tool that helps organizations visualize the most impactful aspects of a process, enabling them to prioritize their efforts and focus on addressing the most significant factors contributing to the overall result.
Leveraging the Pareto Chart enables organizations to concentrate their resources on the few fundamental causes contributing to the majority of the problems, ultimately enhancing overall performance and customer satisfaction.
Business process mapping, a vital tool in Six Sigma, allows organizations to visualize and analyze their business processes, including the production process, using a process map, enabling them to identify areas for business process improvement and optimize their operations.
Creating a visual representation of their processes allows organizations to gain valuable insights into the efficiency and effectiveness of their operations, ultimately driving enhanced performance and customer satisfaction by considering the voice of the customer.
The Project Charter is an essential document in the Six Sigma toolkit, providing a clear definition of project scope and objectives, and serving as a roadmap for project success. Outlining the purpose and goals of a project helps the Project Charter to keep all team members on the same page and ensures that the project stays on track, ultimately contributing to enhanced performance and customer satisfaction.
The RACI Matrix is a valuable Six Sigma tool that helps organizations clarify team member responsibilities and identify gaps in project roles. By outlining the responsibilities of each team member with regard to the tasks associated with the business process, the RACI Matrix enables organizations to ensure that their processes run smoothly and efficiently, ultimately resulting in enhanced performance and customer satisfaction.
Using the RACI Matrix can help organizations ensure that all team members are aware of their
Beyond the core Six Sigma tools, organizations can also leverage additional techniques to analyze, improve, and control quality by reducing defects, such as Statistical Process Control (SPC) and Failure Modes and Effects Analysis (FMEA).
These advanced techniques can further enhance an organization’s ability to:
Statistical Process Control (SPC) is a powerful Six Sigma technique that uses statistical analysis to monitor, measure, and control a process or production method. By collecting and analyzing data, SPC enables organizations to:
Control charts, a key component of SPC, are used to visualize the variation in a process over time and pinpoint when the process is out of control. By implementing control charts and other statistical techniques, organizations can effectively monitor and control their processes, ensuring a high level of quality control and customer satisfaction.
Failure Modes and Effects Analysis (FMEA) is a systematic approach to identifying potential failure modes in a process, product, or system, assessing their impacts, and prioritizing them based on severity. By taking preventive actions to eliminate or reduce these failure modes, FMEA enables companies to improve product quality and reliability. Ultimately, this contributes to enhanced performance and customer satisfaction.
Different Six Sigma certification levels exist to cater to professionals with varying degrees of experience and expertise in the field. Each certification level focuses on a specific aspect of Six Sigma, with higher levels signifying increased proficiency in Six Sigma tools and methodologies.
Obtaining the appropriate certification allows individuals to demonstrate their mastery of Six Sigma tools and contribute to the success of their organization.
The White Belt certification level offers an introductory level of knowledge in Six Sigma, providing individuals with a basic understanding of Six Sigma concepts and tools. While White Belt holders may not lead projects independently, they can still contribute to Six Sigma initiatives by assisting with data collection and other supporting tasks.
The Yellow Belt certification level focuses on more advanced Six Sigma tools and techniques, equipping individuals with the skills necessary to monitor and assess the progress of Six Sigma implementations and provide valuable input to the Six Sigma team.
Yellow Belt holders can play an essential role in driving process improvement and enhancing overall performance within their organization.
The Green Belt certification level emphasizes the complete mastery of Six Sigma tools, allowing individuals to lead individual Six Sigma projects and gather data for analysis.
Green Belt holders possess the skills and knowledge necessary to drive process improvement, optimize operations, and achieve measurable results within their organization.
The Black Belt certification level is geared towards professionals with expert-level knowledge of Six Sigma tools and methodologies. Black Belt holders are capable of directing complex improvement projects, instigating organizational change, and delivering quantifiable outcomes.
By achieving the Black Belt certification, professionals can drive significant improvements in their organization’s performance and customer satisfaction.
The Master Black Belt certification level represents the pinnacle of Six Sigma expertise. Master Black Belt holders demonstrate proficiency in:
In addition to advanced tool mastery, Master Black Belts also possess strong leadership skills.
By achieving the Master Black Belt certification, professionals can lead and mentor others in their organization, driving substantial improvements in performance and customer satisfaction.
Six Sigma tools have been successfully applied across various industries, showcasing their versatility and effectiveness in driving process improvement and enhancing overall performance. In the healthcare industry, for example, Six Sigma tools have been used to enhance quality, address healthcare issues, and improve patient care.
In the field of information technology, Six Sigma tools have been employed to optimize IT support services, software development, and cost and time allocation processes. Similarly, Six Sigma tools have been utilized in the supply chain and logistics industry to enhance efficiency, optimize the order fulfillment process, and implement Lean Sigma methodology.
Selecting the right Six Sigma tools for your organization is pivotal for success. Understanding your organization’s unique needs, goals, and industry-specific requirements allows you to choose the most suitable tools for driving process improvement and enhancing customer satisfaction.
Whether your organization operates in healthcare, information technology, supply chain, or any other industry, the right Six Sigma tools can help you unlock your organization’s full potential and achieve exceptional results.
In conclusion, Six Sigma tools have the potential to revolutionize your organization’s approach to quality control and process improvement. By embracing a data-driven approach, continuous improvement, and mastering the top Six Sigma tools, you can enhance your business processes, minimize defects, and boost customer satisfaction.
As you explore the realm of Six Sigma tools and process optimization, you're likely discovering the tremendous potential these techniques hold for your organization. Imagine harnessing your newfound knowledge and combining it with a proven and structured system that leads you through each step of building a thriving business. That's precisely where the 100 Tasks Company Builder Program excels.
Structured Approach: Just as Six Sigma provides a well-defined approach to process improvement, the 100 Tasks Program offers a detailed roadmap for establishing a successful company. Its three fundamental phases - Setup, Launch, and Scale - seamlessly align with the DMAIC methodology, ensuring that your business growth is systematic and highly efficient.
Comprehensive Guidance: Similar to how Six Sigma tools address various aspects of process improvement, the 100 Tasks Program covers all critical facets of building a successful company.
Martin Bell (Founder & CEO of Bell Ventures) is the visionary and driving force behind the hyper-successful 100 Tasks Startup System which has driven the growth of 20,000+ startups including Zalando and Delivery Hero.
At Rocket Internet, he pioneered the 100-Day-Launch process and led 120+ private and public sector venture-building projects.
Now Martin aims to democratize entrepreneurship by sharing his invaluable practical knowledge and tools to empower aspiring entrepreneurs just like you. Does that sound like you? Then make sure to learn more below ...